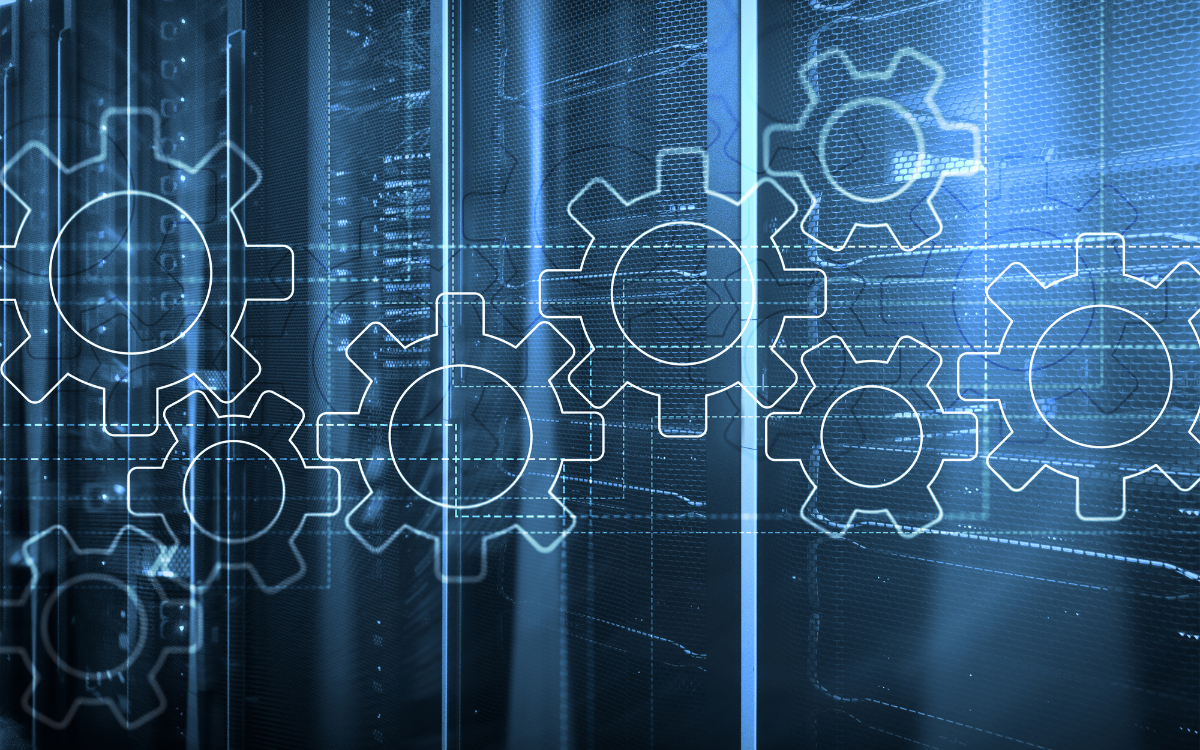
Implementing a robust digital thread manufacturing strategy is paramount for achieving maximum efficiency in the digital transformation era. This approach seamlessly connects product development, production processes, and the entire value chain, revolutionizing traditional manufacturing methods. Manufacturers can optimize product design, streamline workflows, and enhance decision-making by leveraging real-time data and digital twins. The convergence of physical and digital worlds through effective digital thread integration presents an unprecedented opportunity for businesses to drive innovation and remain competitive in today’s rapidly evolving landscape.
Defining the Digital Thread in Modern Manufacturing
Digital Thread in modern manufacturing refers to the seamless integration of digital information throughout the product lifecycle. It connects traditionally siloed stages, from design to production, allowing real-time insights and data flow. Manufacturers can optimize processes, increase efficiency, and enhance decision-making by creating a digital twin of the physical product. This approach transforms product development, leveraging technology to drive maximum efficiency and business value. The effective Digital Thread ensures traceability, agility, and improved ROI across the entire value chain.
The Evolution and Foundations of Digital Thread Technology
Digital Thread Technology has evolved significantly, providing a foundation for seamless integration in manufacturing. Confined initially to product design and development, it extends across the entire value chain. Connecting digital data with physical elements bridges the gap between business systems, ensuring efficient workflow and maximum ROI. This evolution addresses the urgency for agility and traceability in an increasingly digital world, propelling businesses towards automation and enhanced workforce efficiency.
Components of a Digital Thread Framework
Establishing a robust digital thread framework involves integrating key components such as digital twins, real-time data analytics, and automation tools. By connecting product development stages seamlessly, manufacturers can optimize the entire value chain from raw materials to the end product. Ensuring data traceability and agility throughout manufacturing is vital for achieving maximum efficiency and business value. Integrating CAD systems, ERP software, and analytics further enhances workflow efficiency and decision-making capabilities. Stakeholders benefit from improved visibility and collaboration across disparate systems.
The Significance of Digital Thread for Manufacturing Efficiency
In modern manufacturing, the digital thread is pivotal in enhancing efficiency. Providing real-time insights into product data and streamlining production processes ensures maximum efficiency throughout the manufacturing process. This interconnected digital framework bridges the gap between design and production, enabling seamless data flow for informed decision-making. Implementing an effective digital thread strategy empowers manufacturers to optimize workflows, improve agility, and achieve significant ROI, ultimately driving enhanced manufacturing efficiency.
Enhancing Product Design through Real-time Data
Leveraging real-time data in product design processes is crucial for fostering innovation and agility in manufacturing. By integrating digital twin technology and real-time analytics, businesses can optimize product development lifecycles and make informed decisions promptly. This approach enables proactive adjustments based on live insights, minimizing downtime and enhancing overall efficiency. Real-time data empowers product teams to collaborate effectively, swiftly aligning design iterations with market demands. Implementing such practices streamlines design workflows and boosts customer satisfaction through tailored high-quality products.
Streamlining Production Processes
Integrating a digital thread is essential to achieving optimal efficiency in production processes. By connecting all manufacturing phases, from raw materials to the final product, the workflow becomes seamless. Real-time data analytics enable proactive decision-making, identify bottlenecks, and enhance productivity. Automation streamlines repetitive tasks, reducing downtime and improving agility. Stakeholders benefit from improved traceability and workflow visibility across the value chain. Implementing a compelling digital thread aligns the workforce toward maximum efficiency, ensuring a competitive edge in the industry.
Integration Benefits of Digital Thread Across Manufacturing Stages
Bridging the gap between design and manufacturing, the digital thread offers a seamless flow of information across the production process. By achieving this integration, manufacturers can make informed decisions based on real-time data, optimizing efficiency and quality. This interconnected approach enhances the value chain’s transparency, agility, and traceability. Embracing an effective digital thread strategy aligns business systems, product teams, and stakeholders, ensuring a unified approach to manufacturing processes. Streamlining workflows and enhancing collaboration result in improved ROI and workforce productivity.
Bridging the Gap Between Design and Manufacturing
Effective digital thread implementation serves as the bridge between design and manufacturing in modern industries. Manufacturers can optimize the value chain by connecting product development data with the production process. Real-time insights allow for agile adjustments, enhancing product design quality. The synergy of digital twins and automation ensures a seamless workflow from design to production, increasing efficiency and traceability. This integration reduces downtime and significantly improves ROI by aligning business systems with manufacturing goals.
Achieving Seamless Data Integration in Manufacturing
Integrating digital thread technology is paramount to achieving seamless data flow for improved decision-making in manufacturing. Data can flow effortlessly across the value chain by connecting disparate systems and processes through a unified platform. This enables real-time insights into product development and production processes, empowering stakeholders to make informed decisions swiftly. With information technology, businesses can enhance agility and traceability and drive optimal efficiency through data-driven decision-making.
Practical Implementation Examples
Case studies serve as compelling examples of successful digital thread implementation. In the aerospace industry, digital thread integration streamlined processes from design to production, enhancing overall efficiency and reducing costs. Similarly, the automotive sector realized significant gains through digital thread solutions, optimizing supply chain operations, and improving product development timelines. These practical instances showcase the tangible benefits of adopting advanced software tools and technologies to drive digital transformation within manufacturing organizations.
Transforming Automotive Manufacturing with Digital Thread Manufacturing
The automotive manufacturing sector is significantly transforming because of the implementation of digital thread solutions. These solutions integrate product data across the entire value chain, from design to production, ensuring optimal efficiency and traceability. Manufacturers can streamline operations, reduce downtime, and enhance overall agility through real-time access to crucial data points and historical information. This digital transformation enhances productivity, boosts ROI, and ultimately improves customer satisfaction through the timely and precise delivery of high-quality vehicles.
Tools and Technologies for Digital Thread Adoption
Manufacturers must leverage advanced software solutions to adopt a digital thread approach for successful, seamless integration. By utilizing tools like IoT and AI, companies can enhance their digital thread capabilities by optimizing data flow and decision-making processes. Effective implementation of these technologies ensures a smooth transition towards a digitally transformed manufacturing environment, maximizing efficiency and productivity. Embracing these tools empowers organizations to streamline workflows, improve traceability, and achieve a significant return on investment in the digital era.
Facilitating Digital Thread Implementation
Industry-leading software solutions play a pivotal role in seamless Digital Thread integration. Cutting-edge platforms enable real-time data synchronization across the value chain, optimizing product development and production processes. These advanced tools harness the power of digital twins to enhance traceability and agility in manufacturing operations. Businesses in the United States and beyond can achieve maximum efficiency and ROI through sophisticated analytics and workflow automation. Streamlined software applications streamline operations, ensuring effective digital transformation and boosting workforce productivity.
The Role of IoT and AI in Enhancing Digital Thread Capabilities
Integrating IoT and AI plays a pivotal role in enhancing digital thread capabilities. IoT sensors collect real-time data from various stages of the manufacturing process, providing valuable insights for optimization. AI algorithms analyze this data to predict maintenance needs, optimize workflows, and improve efficiency. By leveraging these technologies, manufacturers can achieve a more streamlined production process, reducing downtime, enhancing traceability, and ultimately driving maximum efficiency throughout the value chain.
Adopting a Digital Thread Approach
Ensuring the successful implementation of a digital thread approach requires careful planning and execution. Manufacturers should begin by clearly defining objectives and identifying key stakeholders. Effective team communication is crucial, promoting a unified understanding of the digital thread’s value. Implementing robust IT systems and tools for seamless data flow is essential. Regular training sessions are recommended for employees to maximize understanding and utilization of the digital thread. Continuous monitoring of performance metrics and flexibility to adjust strategies based on outcomes is also vital for long-term success.
Strategies to Ensure a Smooth Digital Thread Integration
One effective strategy to ensure a smooth digital thread integration is conducting thorough training sessions for all stakeholders involved. Educating the workforce on the intricacies of digital thread technology and its benefits fosters a deeper understanding and buy-in from all team members. Creating a detailed roadmap outlining the integration process with clear milestones and timelines helps track progress effectively. Regular communication and feedback loops among product teams and IT specialists ensure alignment throughout the integration journey.
Common Pitfalls in Digital Thread Implementation
Failure to align business systems can hinder digital thread integration. Inadequate stakeholder involvement leads to resistance and inefficiencies. Lack of agile workflows and traceability may disrupt the process. To avoid these pitfalls, emphasize cross-functional collaboration and clear communication. Ensure robust IT infrastructure supports seamless data flow. Address training needs to maximize workforce efficiency. Implement proper change management strategies to mitigate resistance. Regularly assess and refine the digital thread framework for sustained success.
Measuring the Impact of Digital Thread on Manufacturing
Assessing the effectiveness of digital thread implementation in manufacturing involves analyzing key performance indicators (KPIs) for efficiency. Manufacturers can quantify the benefits by evaluating metrics such as production cycle time reduction, cost savings, and improved quality control. Additionally, long-term advantages like enhanced agility and traceability throughout the value chain contribute to a comprehensive understanding of the return on investment (ROI) from a well-executed digital thread strategy. Tracking these metrics ensures continuous improvement and maximizes efficiency within the manufacturing process.
Key Performance Indicators for Digital Thread Efficiency
Utilize key performance indicators (KPIs) to measure the effectiveness of your digital thread implementation. Monitor metrics like lead time reduction, cycle time improvement, and overall equipment effectiveness (OEE) to gauge efficiency enhancements. Analyze data on production uptime, workflow optimization, and error rates for a comprehensive view of operational success. Incorporate real-time feedback loops to ensure continuous improvement and adaptability. By tracking these indicators through a strategically implemented digital thread, manufacturers can drive productivity, quality, and profitability.
Long-term Benefits of Implementing a Digital Thread Strategy
Improved operational agility, enhanced traceability, and streamlined workflows are enduring advantages of embracing a digital thread strategy in manufacturing. Long-term benefits include optimized product development cycles, reduced downtime, and increased ROI through informed decision-making. By integrating historical data and real-time insights, organizations can achieve maximum efficiency and customer satisfaction while future-proofing their business against evolving industry trends. The strategic implementation of a digital thread approach establishes a foundation for sustained growth, aligning business systems and empowering workforce agility.
Future Trends in Digital Thread and Manufacturing
The future of Digital Thread in manufacturing is poised for exciting advancements. As technology progresses, we anticipate enhanced integration of digital twins, automation, and analytics to optimize production processes further. The focus will shift towards increased traceability, agility, and efficiency throughout the value chain. Businesses can expect improved ROI, workforce productivity, and customer satisfaction through effective digital thread implementation. Embracing these upcoming trends will undoubtedly revolutionize the manufacturing landscape, paving the way for unprecedented efficiency and innovation.
Predictions on the Evolution of Digital Thread Technologies
Advancements in digital thread technologies are expected to increase automation and agility within manufacturing processes. Integrating digital twins and IoT will revolutionize traceability and workflow efficiency across the value chain. AI-driven predictive analytics will enable proactive decision-making, reducing downtime and enhancing workforce productivity. The future evolution will focus on real-time insights, ensuring maximum efficiency and ROI. Stakeholders can anticipate a seamless digital transformation, aligning business systems for enhanced value.
Preparing for the Next Wave of Manufacturing Innovations
Embracing the upcoming surge of manufacturing innovations necessitates proactive steps in digital thread adoption. Manufacturers must focus on integrating advanced tools like IoT and AI for enhanced digital thread capabilities. By aligning business systems and supply chain processes, companies can achieve higher agility and traceability in their operations. Anticipating these future trends enables organizations to stay ahead in the digital transformation race, ensuring maximum efficiency and significant ROI. A forward-looking approach to technology integration will drive success amidst evolving industry landscapes.
Conclusion
In conclusion, implementing a robust digital thread strategy is paramount for modern manufacturing to achieve maximum efficiency and competitiveness. Businesses can optimize their entire value chain by integrating digital twin technology, real-time data analysis, and streamlining production processes. This approach enhances product development and increases agility, traceability, and ROI. Embracing digital transformation with advanced tools and technologies paves the way for a future where the industry thrives on innovation and interconnected systems.
Frequently Asked Questions
What Are the First Steps to Implementing a Digital Thread?
Identifying key processes, selecting appropriate digital tools, and establishing data integration protocols are crucial initial steps in implementing a Digital Thread framework.
How Does Digital Thread Differ from Digital Twin Technology?
Digital Thread focuses on the flow of data across the entire product lifecycle, while a Digital Twin replicates a physical product digitally to monitor and analyze its performance. While Digital Thread emphasizes data connectivity, Digital Twin recreates a virtual model for real-time insights.