In the fiercely competitive manufacturing world, reducing costs without compromising product quality is paramount. Manufacturers constantly seek strategies to streamline their systems, reduce production costs, and increase profitability. However, the challenge lies in identifying cost-reduction methods that do not sacrifice product quality or customer satisfaction. This article explores the concept of cost-effective manufacturing and how Rapid Waterjet Design (RWD) can help manufacturers achieve savings and maintain quality.
Manufacturing costs encompass the sum of all resources used to procure raw materials and convert them into finished products. These include direct material costs, direct labor costs, and production overheads. While it is challenging to maintain quality and reduce manufacturing costs simultaneously, manufacturers must focus on improving product quality, business efficiency, and profits.
Rapid Waterjet Design (RWD) is a manufacturing approach that embraces cost-effective strategies while ensuring product quality. By leveraging advanced technology, cutting-edge machinery, and automation, RWD aims to reduce production costs without compromising the final product. This article will delve into the philosophy behind RWD, its role in balancing quality with cost-effectiveness, and its impact on the manufacturing process.
Embracing RWD’s Cost-Effective Manufacturing
In today’s competitive manufacturing landscape, embracing cost-effective strategies is critical. Rapid Waterjet Design (RWD) offers a solution by incorporating cost-reduction strategies into manufacturing. By implementing lean manufacturing principles, leveraging advanced technology, and optimizing production processes, RWD enables manufacturers to reduce manufacturing costs while maintaining product quality. This article explores the benefits and strategies of RWD’s cost-effective manufacturing approach.
The Philosophy Behind Rapid Waterjet Design (RWD)
At the core of Rapid Waterjet Design (RWD) lies the philosophy of lean manufacturing principles. RWD embraces the concept of continuous improvement and aims to eliminate waste in the manufacturing process. RWD maximizes efficiency and reduces costs by identifying non-value-added activities and streamlining production processes.
One of the most effective ways RWD reduces costs is by eliminating waste. Waste can take various forms, including inventory, overproduction, transportation, waiting time, defects, overprocessing, and wasted talent. By identifying and eliminating these wastes, RWD can significantly reduce manufacturing costs.
Additionally, RWD encourages collaboration and engagement among team members to continuously improve processes. RWD fosters a culture of innovation and efficiency by involving employees in the decision-making process and empowering them to suggest improvements.
Overall, the philosophy behind RWD is to optimize the manufacturing process by focusing on lean principles and continuous improvement. By embracing effective ways to reduce waste and maximize efficiency, RWD enables manufacturers to achieve cost-effective manufacturing while maintaining product quality.
How RWD Balances Quality with Cost-Effectiveness
One of the main concerns regarding cost reduction in manufacturing is balancing it with product quality. Rapid Waterjet Design (RWD) addresses this challenge by incorporating cost-effective strategies without compromising quality.
RWD achieves this balance by leveraging advanced technology and efficient manufacturing processes. Using cutting-edge machinery and automation, RWD reduces labor costs and minimizes the risk of human error, ensuring consistent product quality. This improves efficiency and reduces the need for costly rework or product recalls.
Furthermore, RWD optimizes production processes to reduce material waste and streamline operations. By identifying and eliminating non-value-added activities, RWD minimizes production costs while maintaining high-quality standards.
Overall, RWD’s approach to cost-effective manufacturing ensures that manufacturers can achieve savings without sacrificing the quality of their products. By leveraging technology, optimizing processes, and focusing on quality, RWD strikes the right balance between cost-effectiveness and product quality.
The Role of Advanced Technology in RWD’s Manufacturing Process
Advanced technology is crucial in Rapid Waterjet Design (RWD)’s manufacturing process. By incorporating cutting-edge technology, RWD enables manufacturers to reduce production costs and improve efficiency.
Manufacturing companies can leverage advanced technology in various ways to achieve cost reduction. For example, implementing automation systems can significantly reduce labor costs and increase production efficiency. Predictive maintenance programs can minimize machine downtime, reduce overhead costs, and maximize efficiency.
Additionally, RWD’s use of advanced technology allows for greater precision and accuracy in the manufacturing process, resulting in higher product quality and reduced material waste. Manufacturers can achieve cost-effective production by leveraging the latest technological advancements without compromising quality.
Leveraging Cutting-Edge Machinery for Efficiency
One critical factor in achieving cost-effective manufacturing with Rapid Waterjet Design (RWD) is the use of cutting-edge machinery. By leveraging advanced technology, RWD enables manufacturers to improve efficiency and reduce costs in the production process.
Here are some ways in which RWD leverages cutting-edge machinery to achieve efficiency:
- Machine time efficiency: RWD focuses on optimizing machine utilization to minimize downtime and maximize production output. By reducing machine idle time, manufacturers can reduce production costs and improve overall efficiency.
- Reduced direct labor: By using automated systems and advanced machinery, RWD minimizes the need for direct labor, reducing labor costs and increasing productivity.
- Energy efficiency: Cutting-edge machinery often incorporates energy-saving features, reducing energy consumption and lowering energy costs for manufacturers.
By leveraging cutting-edge machinery, RWD enables manufacturers to achieve cost-effective manufacturing by optimizing machine time efficiency, reducing direct labor costs, and improving energy efficiency.
The Impact of Automation on Production Costs and Quality
Automation plays a significant role in Rapid Waterjet Design (RWD) by reducing production costs and improving product quality. By implementing automated systems, manufacturers can achieve cost-effective manufacturing without compromising quality.
Automation reduces production costs by minimizing overhead expenses and improving overall efficiency. By automating repetitive tasks, manufacturers can reduce the need for manual labor and decrease labor costs. Additionally, automation reduces the risk of human error, improving the accuracy and consistency of the manufacturing process.
Furthermore, automation enhances quality control by ensuring consistent production standards. Automated systems can perform quality checks and inspections faster and with greater accuracy than manual processes. This reduces the risk of defects and product recalls, ultimately improving product quality and reducing costs associated with rework.
Overall, automation positively impacts production costs and quality in RWD’s manufacturing process. By reducing labor costs, improving efficiency, and enhancing quality control, automation enables manufacturers to achieve cost-effective manufacturing without compromising product quality.
Strategies for Optimizing Production Processes
Optimizing production processes is a key strategy for achieving cost-effective manufacturing. Rapid Waterjet Design (RWD) focuses on implementing strategies that streamline operations and reduce manufacturing costs.
Here are some effective strategies for optimizing production processes:
- Implementing machine time efficiency: By reducing lead times and maximizing machine utilization, manufacturers can minimize indirect costs and improve production efficiency.
- Leveraging bulk material purchasing: By purchasing materials in bulk, manufacturers can benefit from economies of scale and reduce material costs. This strategy also helps streamline inventory management and minimize supply chain disruptions.
- Streamlining operations with in-house CNC machining: By bringing CNC machining capabilities in-house, manufacturers can reduce outsourcing costs, improve production efficiency, and gain better control over the supply chain.
By implementing these strategies, manufacturers can optimize production processes, reduce manufacturing costs, and enhance overall profitability.
Implementing Machine Time Efficiency
Implementing machine time efficiency is critical in achieving cost-effective manufacturing. Manufacturing companies can reduce overhead expenses and enhance productivity by optimizing production schedules and minimizing idle time. Efficient use of machinery ensures maximum output with minimal downtime, thereby improving the operation’s cash flow and overall profitability. This strategic approach to production activities reduces lead times and enhances the business’s competitiveness in the market. Streamlining machine time is vital in driving continuous improvement and cost-reduction efforts.
The Benefits of Bulk Material Purchasing
Bulk material purchasing offers substantial cost advantages by enabling economies of scale, reducing overall material costs, and minimizing procurement expenses. By buying in larger quantities, manufacturing companies benefit from lower unit costs, streamlined supply chain management, and improved cash flow. This strategic approach cuts down on production costs and ensures a steady supply of raw materials, enhancing production efficiency and overall cost savings.
Streamlining Operations with In-House CNC Machining
Streamlining operations with in-house CNC machining can significantly enhance efficiency and cost-effectiveness in manufacturing processes. By managing production activities internally, companies can reduce lead times and overhead expenses associated with outsourcing. Implementing CNC machining allows for precise control over production costs and quality standards, ultimately improving the overall manufacturing operation. This strategic approach optimizes workflow, minimizes material waste, and enhances product development capabilities, leading to increased savings and streamlined operations.
Reducing Costs Without Compromising Quality
Utilizing efficient cost-reduction strategies is crucial in maintaining quality standards. Focusing on manufacturing operations, supply chain management, and lean principles allows it to streamline processes and minimize expenses without sacrificing product excellence. Implementing stringent quality control measures alongside cost-saving initiatives ensures that the final output meets the desired standards while maximizing cost efficiencies. Striking a balance between reducing overhead costs and upholding product quality is a core tenet of sustainable manufacturing practices.
The Significance of Quality Control in Cost Reduction
Implementing rigorous quality control measures within manufacturing processes is a cornerstone of cost reduction strategies. Ensuring that each product meets specified standards decreases the need for rework or replacement, leading to significant savings in production costs. Quality control also enhances the overall efficiency of the manufacturing operation by minimizing errors and waste. Embracing a high-quality culture reduces costs associated with defects and fosters customer satisfaction, ultimately boosting profitability and competitiveness.
Case Studies: Success Stories of RWD’s Approach
Discover how RWD’s approach revolutionized manufacturing with real-world case studies showcasing significant cost savings and enhanced quality. RWD successfully reduced manufacturing costs by leveraging Lean principles and optimizing production processes while maintaining top-notch standards. These success stories highlight the effectiveness of implementing innovative strategies to streamline operations, minimize waste, and maximize efficiency, setting a benchmark for industry-sustainable and cost-effective manufacturing practices.
Leveraging Lean Manufacturing Principles
Embracing lean manufacturing principles is crucial for efficient and cost-effective production. Companies can optimize their manufacturing processes by eliminating waste and focusing on value-added activities. Lean principles emphasize continuous improvement, reducing lead times, and enhancing productivity. Implementing lean methodologies streamlines operations, minimizes costs, and improves product quality. This approach enhances efficiency and fosters a culture of innovation and problem-solving within manufacturing companies. Leveraging lean manufacturing principles is instrumental in driving sustainable growth and competitive advantage in the industry.
The Essentials of Lean Manufacturing in RWD
Lean manufacturing in RWD focuses on streamlining production by eliminating waste and optimizing efficiency. By implementing lean principles, RWD minimizes unnecessary costs while enhancing overall quality. This approach involves continuous improvement and eliminating all forms of waste, ensuring that every aspect of the manufacturing process adds value. Through lean manufacturing, RWD emphasizes the importance of efficient resource utilization and maintaining high productivity across its operations.
Real-World Applications of Lean Principles at RWD
At RWD, implementing lean principles translates to tangible benefits in real-world scenarios. RWD enhances operational efficiency and cuts unnecessary costs by optimizing inventory management and reducing waste. The strategic application of lean manufacturing techniques streamlines production processes, boosts productivity, and ensures resource utilization is at its most effective. RWD’s commitment to continuous improvement through these lean principles enhances their bottom line and sets a benchmark for sustainable and cost-effective manufacturing practices.
The Future of Manufacturing with RWD
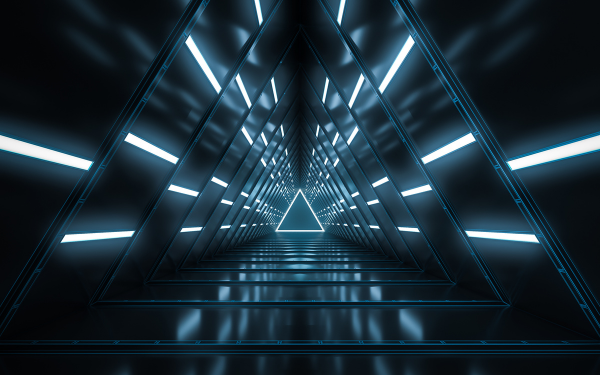
Harnessing cutting-edge technology, RWD is poised to revolutionize the manufacturing landscape. Predicting advancements in technology and expanded cost-effective manufacturing methods, RWD is at the forefront of innovation in sustainable manufacturing practices. As supply chains evolve, RWD’s commitment to eco-friendly production techniques will enhance its competitive edge in the market. Embracing the future with RWD promises cost savings and a greener approach to manufacturing, setting new benchmarks for the industry.
Predictions for Technological Advancements
The manufacturing industry is poised for significant technological advancements in the coming years. Automation, AI integration, and advanced data analytics will revolutionize production processes. Predictive maintenance using IoT sensors will become commonplace, reducing downtime and enhancing operational efficiency. Virtual and augmented reality technologies will streamline product design and development phases, accelerating time-to-market. Blockchain applications in the supply chain will ensure transparency and traceability, boosting overall efficiency. These advancements highlight a promising future for cost-effective manufacturing with sustainable, cutting-edge solutions.
Expanding the Reach of Cost-Effective Manufacturing
By expanding the reach of cost-effective manufacturing, companies can tap into new markets and enhance profitability. Leveraging efficient supply chains and optimizing production processes are integral steps in reaching a wider audience. Implementing lean manufacturing principles can drive down costs while maintaining quality standards. Embracing technology and automation can further amplify the scope of cost-effective manufacturing techniques. The goal is to extend these strategies across various sectors to maximize savings and improve overall competitiveness in the market.
The Environmental Impact of RWD’s Manufacturing Techniques
RWD’s manufacturing techniques prioritize sustainability by minimizing energy costs and material waste. By implementing eco-friendly practices, RWD reduces overhead expenses and demonstrates a commitment to environmentally conscious manufacturing. This approach aligns with the industry’s growing emphasis on sustainable strategies, showcasing how cost-effective manufacturing can coexist with eco-friendly initiatives. Mitigating environmental impact through efficient processes is a core principle of RWD, positioning the company as a leader in responsible manufacturing practices.
Sustainable Practices in Cost Reduction
Implementing sustainable practices in cost reduction involves optimizing energy usage, reducing material waste, and minimizing environmental impact. By adopting eco-friendly manufacturing techniques, companies can cut overhead expenses, enhance their brand image, and contribute to a greener future; from streamlining production processes to utilizing renewable resources, incorporating sustainability into operations benefits both the bottom line and the planet. Embracing sustainability is a strategic move towards long-term cost savings and corporate responsibility.
RWD’s Commitment to Eco-Friendly Manufacturing
RWD prioritizes eco-friendly manufacturing by minimizing waste and optimizing resource usage. RWD strives to lessen its environmental footprint through sustainable practices, such as efficient waste management and reduced energy consumption. By integrating green initiatives into its production processes, RWD reduces costs and contributes to a cleaner environment. This commitment aligns with RWD’s ethos of responsible manufacturing, showcasing how cost-effective strategies can coexist with environmentally conscious practices.
Contact Us To Start Your Project Today!
Frequently Asked Questions
How Does RWD Ensure Quality While Reducing Costs?
RWD ensures quality while reducing costs by integrating advanced technology like efficient machinery and automation. Strategies such as machine time optimization and bulk material purchasing further enhance cost-effectiveness without compromising quality control. Case studies demonstrate successful implementation, showcasing RWD’s commitment to excellence.
What Technologies Has RWD Adopted to Improve Efficiency?
RWD has adopted various cutting-edge technologies to improve efficiency in its manufacturing operations. This includes the implementation of automated systems, predictive maintenance programs, and data analytics. These technologies enable RWD to optimize production processes, reduce downtime, and improve overall operational efficiency.
Can RWD’s Strategies Be Applied to Other Industries?
Yes, RWD’s cost-effective manufacturing strategies can be applied to other industries. The principles of lean manufacturing, strategic adaptation, and continuous improvement are universally applicable and can be customized to suit the specific requirements of different industries. By implementing these strategies, manufacturers in various industries can achieve significant cost reductions and improve overall efficiency.
How Does RWD’s Approach to Manufacturing Contribute to Sustainability?
RWD’s approach to manufacturing prioritizes sustainability through the implementation of sustainable practices, such as resource conservation and waste reduction. By minimizing environmental impact and conserving resources, RWD contributes to a more sustainable future while achieving cost-effective manufacturing.
What Measures Does RWD Take to Stay Ahead in a Competitive Market?
RWD takes several measures to stay ahead in a competitive market. This includes leveraging our competitive advantage through cost-effective manufacturing, staying updated on market trends, fostering innovation, prioritizing customer satisfaction, and continuously improving its manufacturing processes through lean manufacturing principles. These measures enable RWD to maintain its position as an industry leader and stay ahead of the competition.